The force-displacement software module (FDM) was designed to record and monitor the the processes involved in building camshafts joining processes of camshafts. It ensures seamless quality assurance. The software is now running at various production sites worldwide and ensures that the data relevant to the quality of the camshafts produced are recorded and documented without gaps.
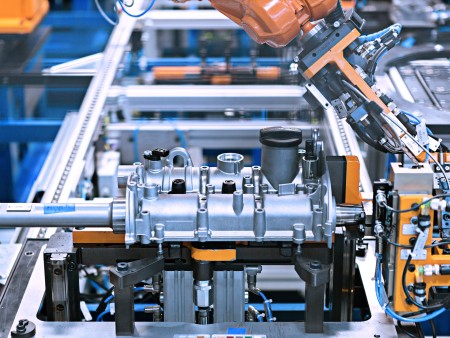
The customer
Thyssenkrupp Camshafts is one of the most successful developers and manufacturers of integrated camshafts, valve train components and cylinder head covers. It is thus considered a successful, innovative partner to the international automotive industry. Producing over 30 million camshafts per year at 10 locations, thyssenkrupp is the global market leader in this sector.
The task
The idea for the project stemmed from the replacement of the previous FDM software. The purpose of the new solution was to completely replace the existing one and offer an advanced and more convenient scope of functions. For example, a FDM multi-channel capability or the integration of data analysis directly in the FDM. In the past, thyssenkrupp Presta TecCenter AG developed additional software components which were no longer compliant with the legacy FDM. These tools also needed to be supported by the new FDM. Another important requirement was that the FDM should also be capable of operation on camshaft setters with limited computer resources and potentially with an older operating system. Therefore, the technologies used needed to be specified in a way that met this requirement.
The solution
The software development was realised in close collaboration with the project manager of thyssenkrupp Presta TecCenter AG and the production team at company headquarters in Ilsenburg. Agile development was applied, in that prototypes of the software were tested at short, periodic intervals. Using these test results, it was possible to immediately implement changes and eliminate any errors.
Easy to handle
Since the developers of the original software were no longer contactable, the implementation proved to be complex. To ensure that the new FDM is usable for both new as well as older systems, the following technologies were used: C#, .NET Framework 3.5, Windows Forms, WCF and SQLite.
Placing the cams is a time-critical step. Therefore, it is enormously important that the analysis of the data by the FDM is performed very fast. This was verified with various tests on the camshaft placers and validated by performance tests during the development process. In addition, it is fundamental that the core process logic is separate from the user interface, so that a service logs the data without any interruptions. The analysis of the measured displacement and force data was previously handled only by a PLC. This procedure, however, had some limitations in terms of storage capacity and performance. With a new PC-based software solution, an application was developed that has almost unlimited memory capacity at its disposal. The FDM multi-channel function also allows data from multiple cam placers to be recorded, analysed and visualised in a central user interface with just one FDM.
Data evaluation is an additional powerful feature of the FDM which was integrated into the tool as part of the new development. Different analysis methods may be defined in the FDM using a plug-in system. A user-friendly and well-structured configuration interface allows the operator to select a specific analysis method for each cam assembled in the FDM. The fact that the analysis methods are easy to define and extend is another significant advantage for the user.
Reliable and user-friendly
Due to the high demands placed on software tools such as the FDM, the requirements for quality assurance, handling and flexibility are fundamentally different from the state of the art 20 years ago. Developed in collaboration with Solve, the new FDM is a powerful tool that guarantees consistent data collection and is easy to use. It therefore completely fulfilled the customer’s wishes.
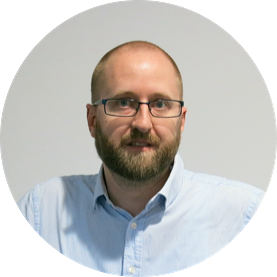
“Solve has been significantly responsible for the establishment of a commercially viable version of the FDM software. It has provided us with excellent, professional and highly committed support in terms of concept, technology and methodology during the entire process.”
Markus Winkler
Project-Leader
thyssenkrupp Presta TecCenter AG